BHP Cage Winder Upgrade
Nickel Mine
Leinster, WA
The Cage Winder at Leinster is the designated “secondary means of egress” for the mine. It consists of a “100 man” cage with counterweight. The Cage is used to transport the workforce into and out of the mine each shift to minimize transport time and maximise production time.
Key criteria - Safe, shortest change-over option
Winder - Double Drum, Cage and counterweight, Mine depth 1,100m with 13 operating level
Scope - Winder DC drive, Brake System, Control System, Safety System
How - To facilitate the shortest shutdown possible, a new equipment room was built and all equipment installed. This allowed the full winder systems to be pre-commissioned prior to shutting down the winder.
Learn more about the Project Scope here.
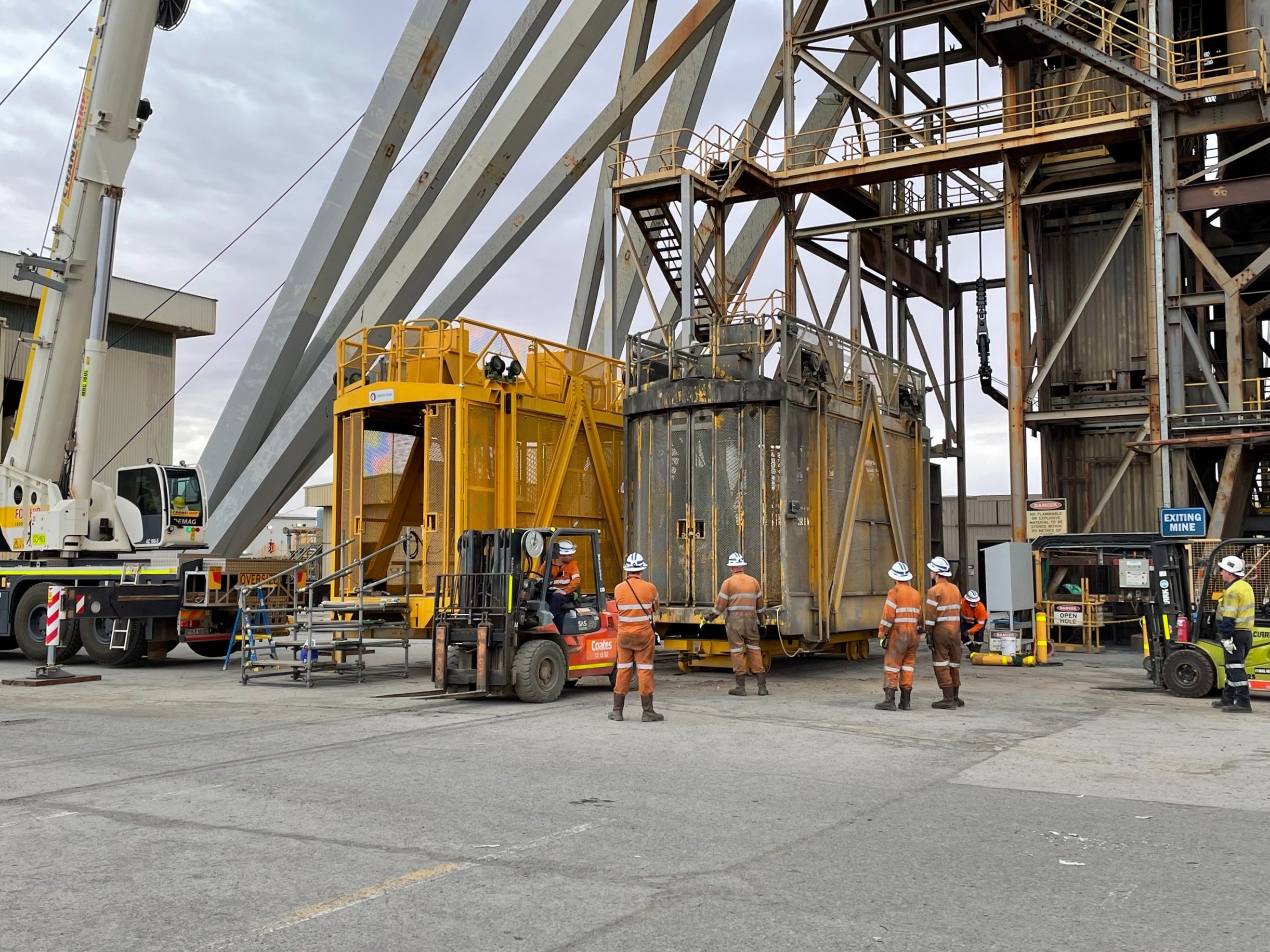
New Conveyance Install
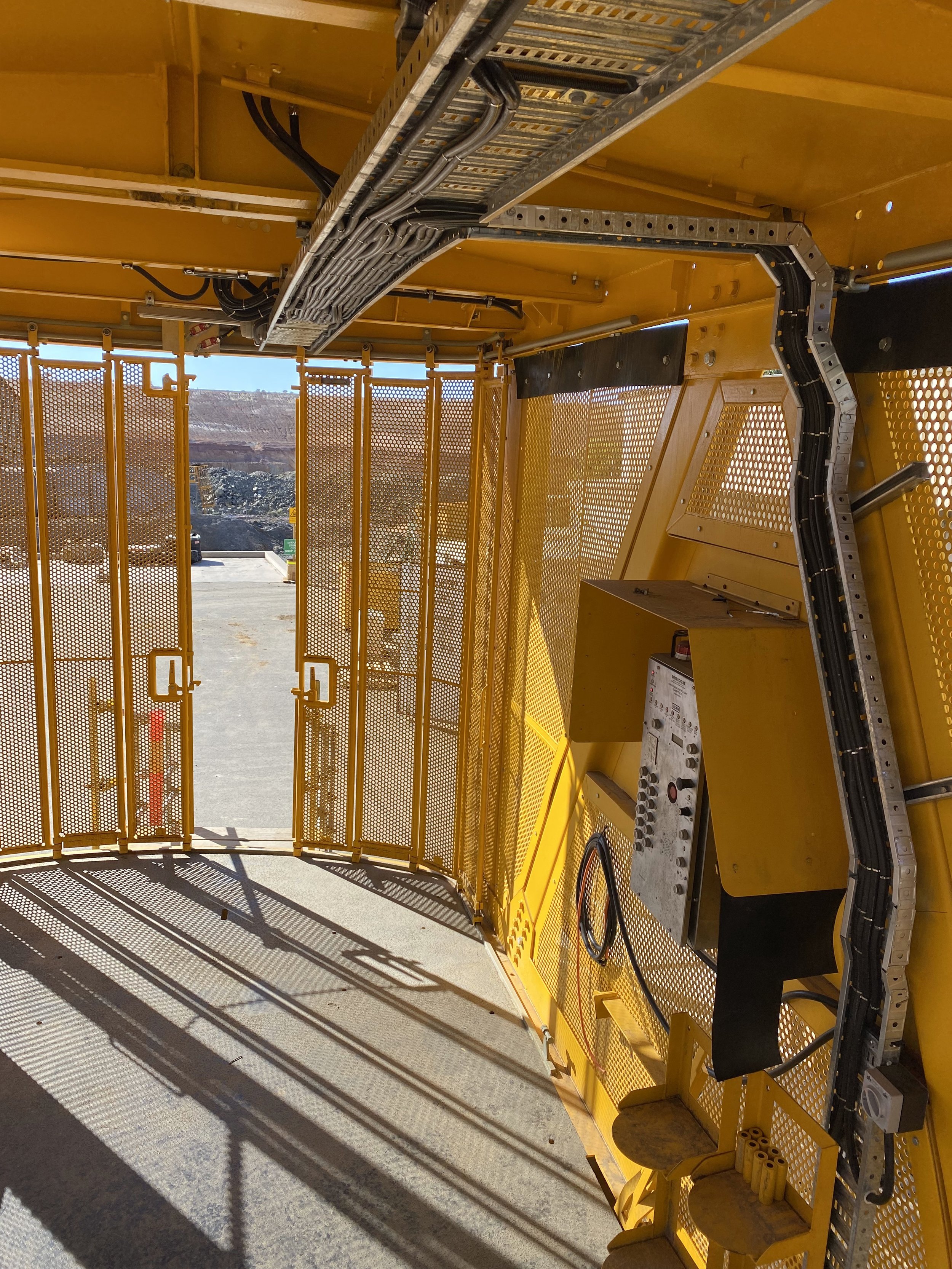
Conveyance Fit Out
Driver Station Development
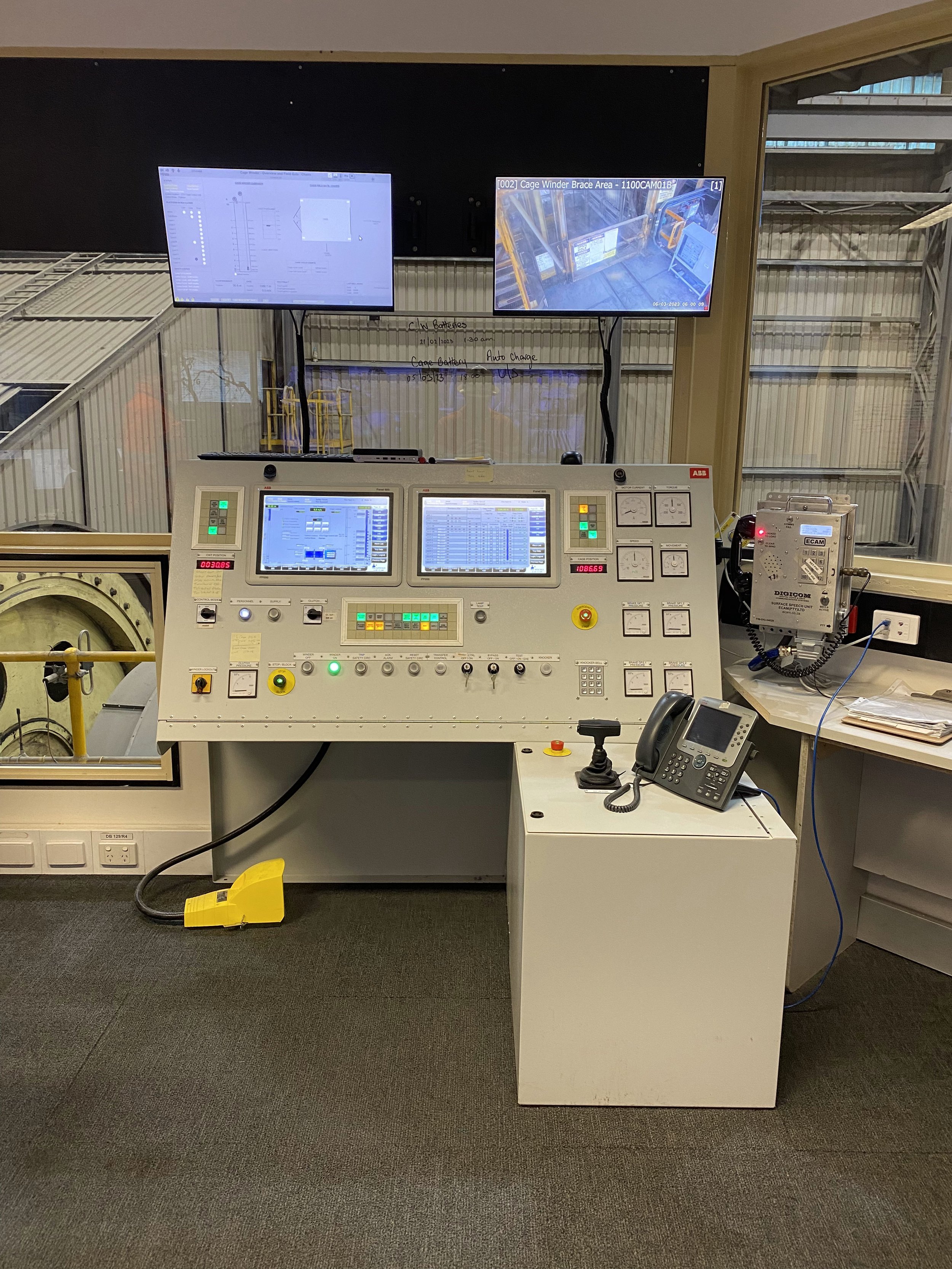
Final Driver Station
Before - Break and Clutch HPU
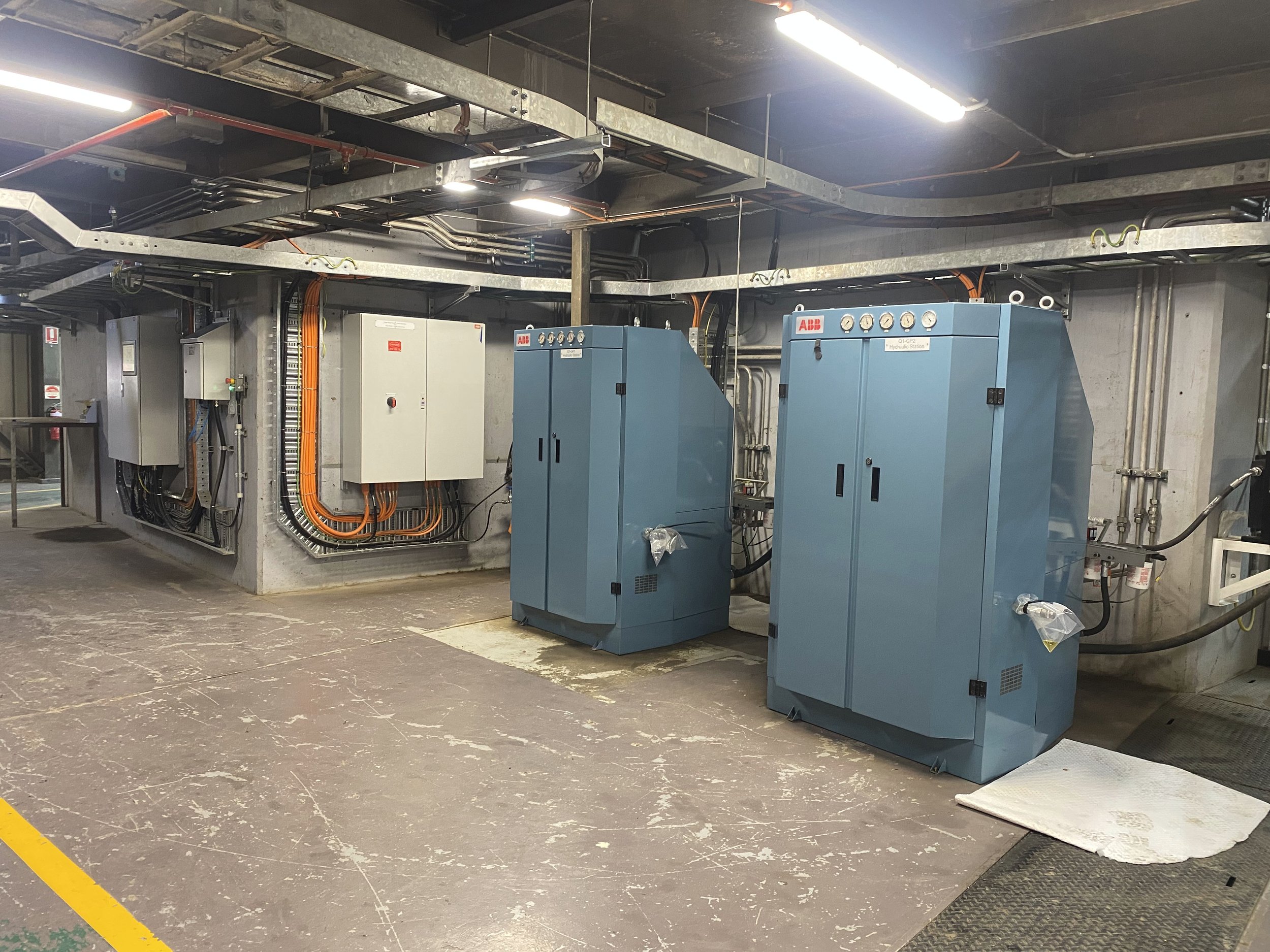
After - Break and Clutch HPU
Before - Converter Room Upgrade
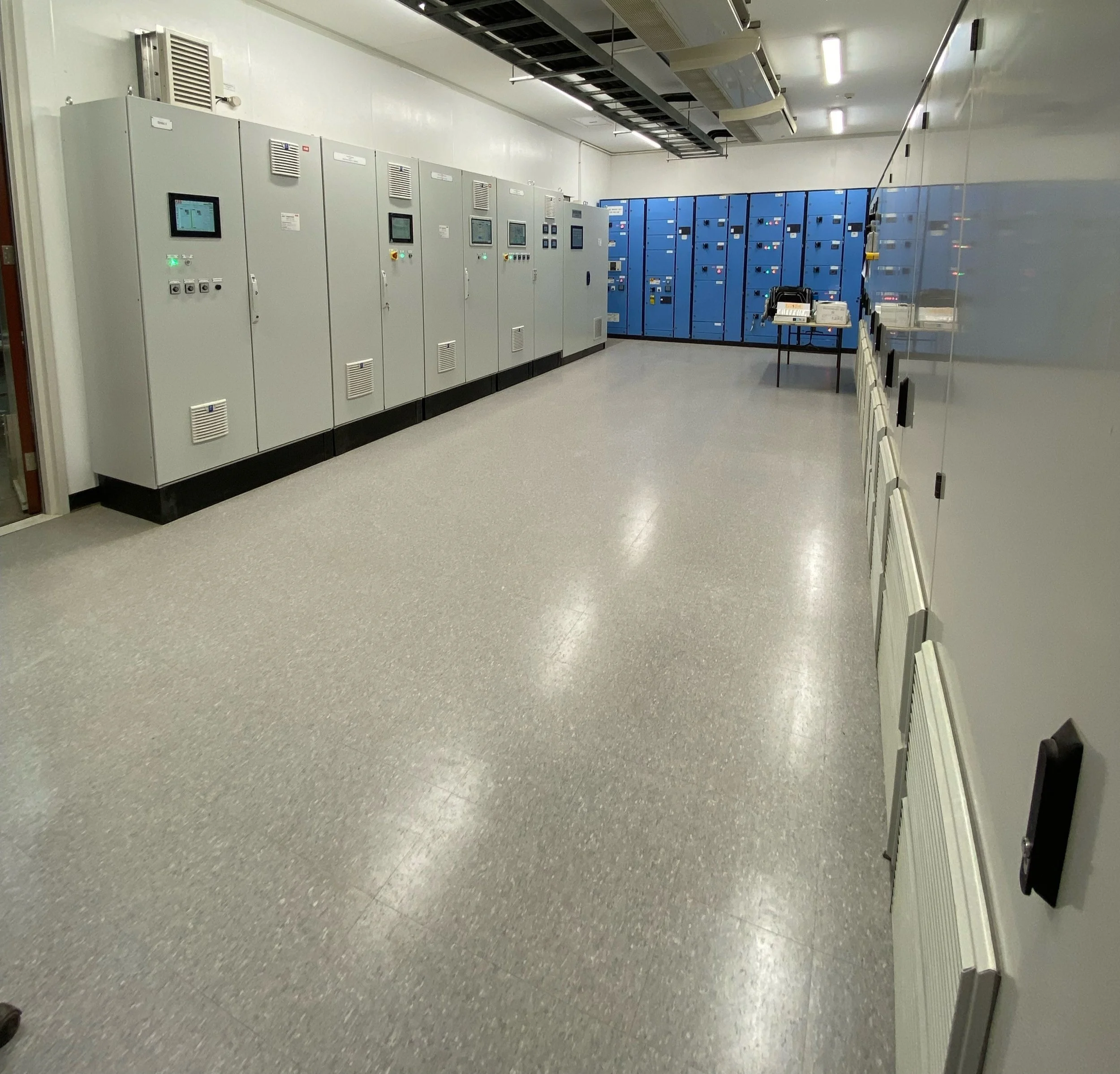
After - Converter Room Upgrade
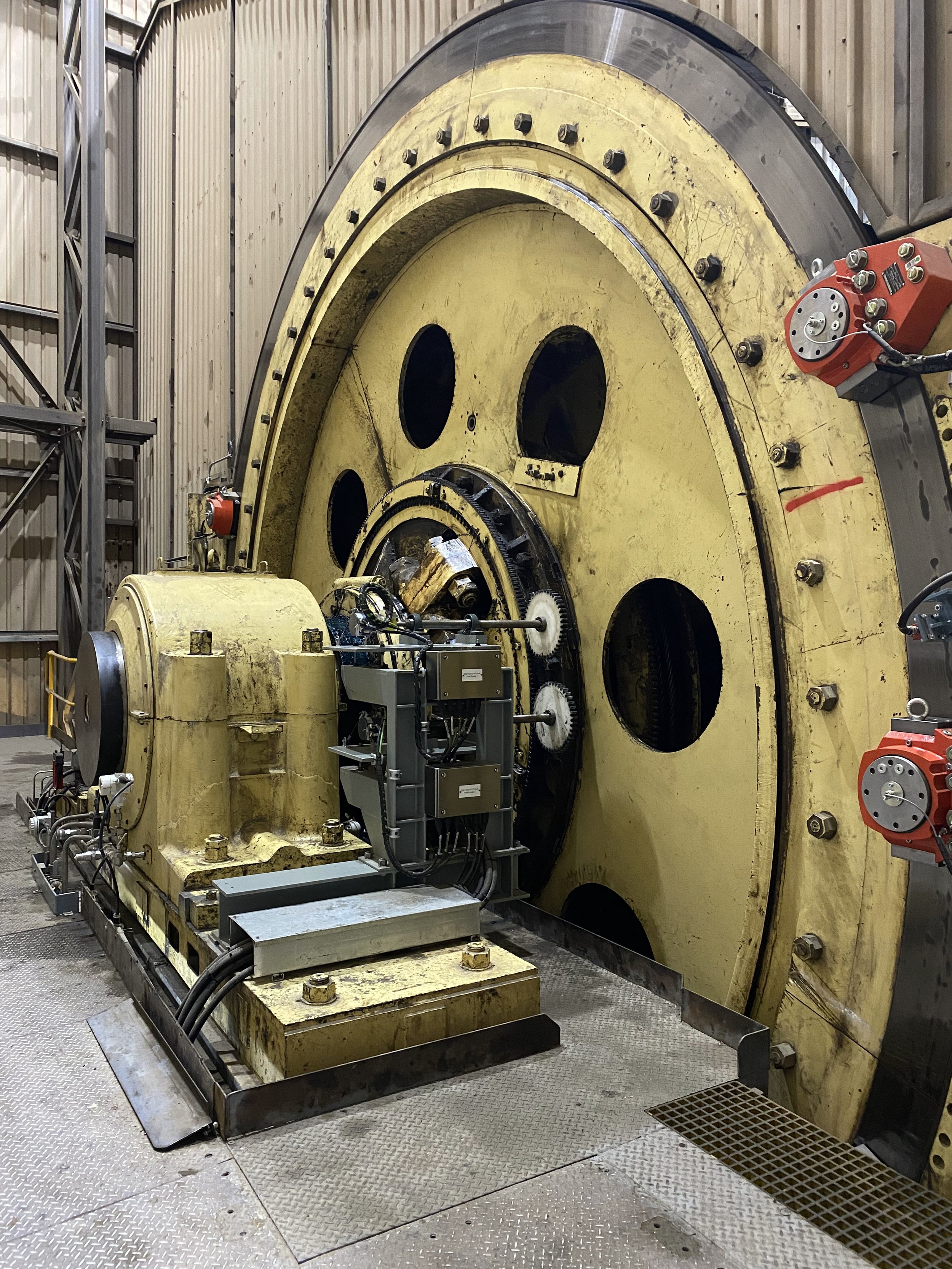
Clutched Drum Position Monitoring Encoders
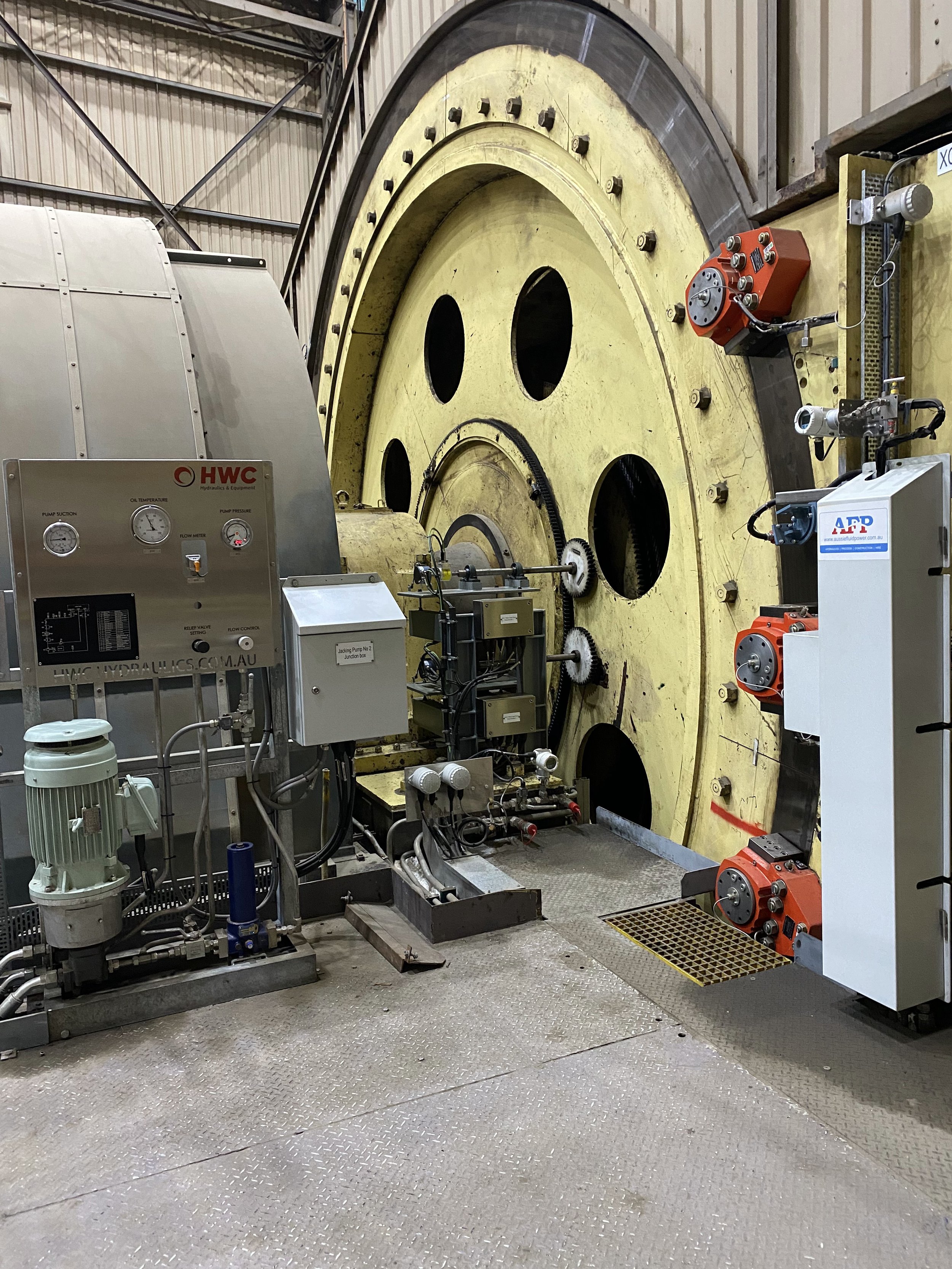
Fixed Drum Position Encoders
Project Scope
-
New Safety System
Complete Brake System replacement including callipers
Control System replacement
Conveyance communication system replacement including battery charging system
HV switchboard replacement
LV MCC replacement
ELV control supply replacement
Communication network modifications for the new systems
Complete winder driver control room refurbishment
De-construction of obsolete infrastructure to free-up space required for the project
-
Manage and coordinate Winder System vendor design and delivery
Coordinate Safety System specialist design and audit work
Manage and coordinate all site installation work
Coordination of all project work with site operations to minimise project impact
Manage and coordinate all logistics for project equipment and personnel
Manage all documentation and review activities
Complete upgrade was audited and verified to AS61508 compliance
Project delivered safely with no injuries